Introduction
CNC (Computer Numerical Control) machining technology is widely used in manufacturing, enabling both high precision and high efficiency in production. However, in practical production processes, precision and efficiency are often two opposing goals. While striving for higher precision, production efficiency may be affected, and vice versa. How to strike a balance between these two is a key challenge in CNC machining technology.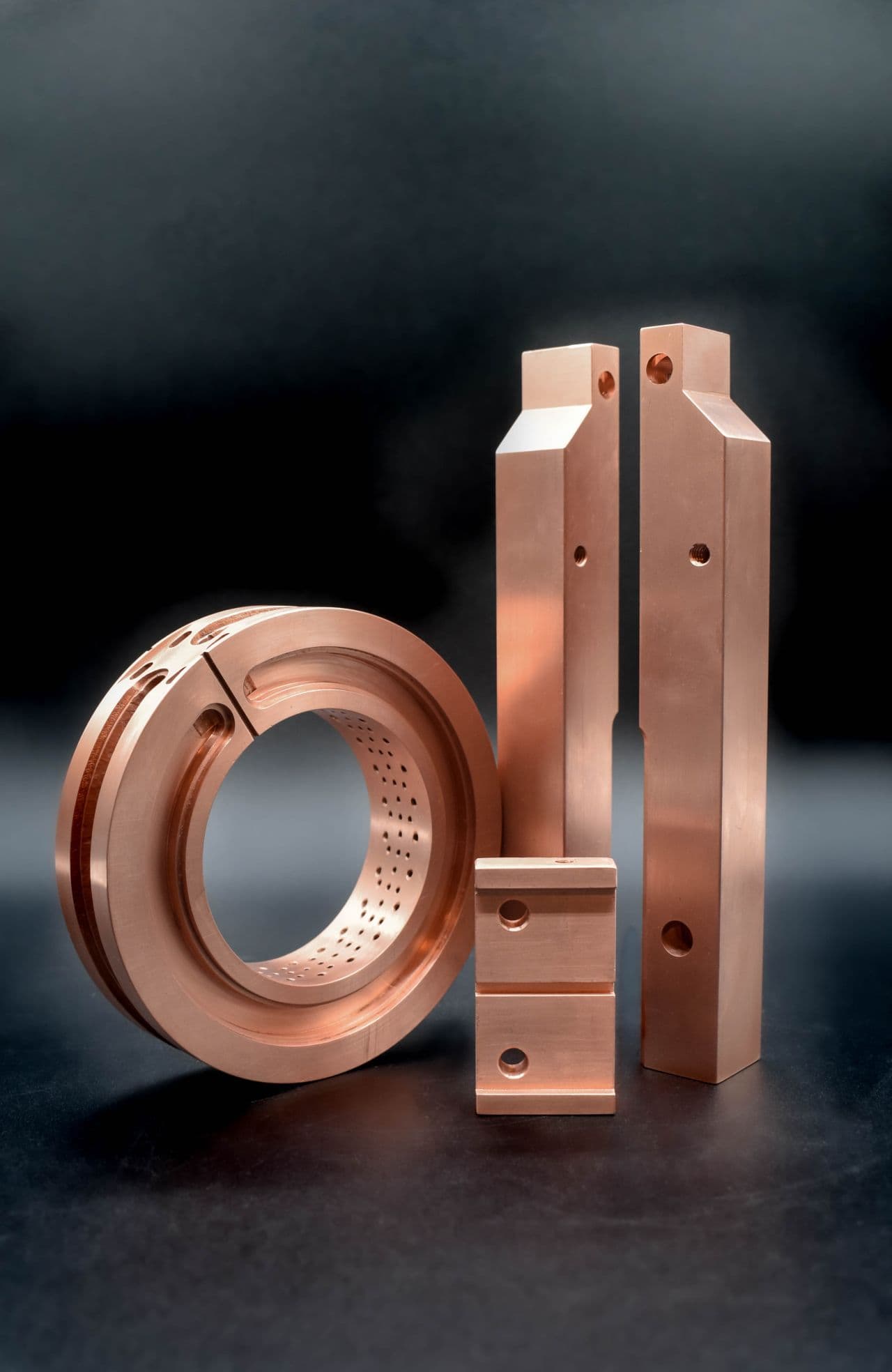
The Relationship Between CNC Machining Precision and Efficiency
In CNC machining, precision typically refers to the degree of alignment between the geometry of the workpiece and the design blueprint. High precision machining ensures the quality and functionality of parts, but it usually requires more time to complete. Efficiency, on the other hand, refers to the quantity or speed of production within a given time frame. In many cases, to improve efficiency, some precision may be sacrificed, leading to errors in the workpiece.
- Impact of Precision Requirements: High precision machining generally requires high-quality tools, advanced machine tools, and more refined processing techniques. These factors increase machining time and reduce production efficiency.
- Measures to Improve Efficiency: To increase efficiency, higher cutting speeds and larger feed rates are often employed, which may affect the workpiece's precision. Therefore, it is crucial to find a way to improve efficiency while maintaining high precision.
How to Balance Precision and Efficiency
-
Choosing the Right Machine Tool and Cutting Tools
- Case Study: For instance, a GT parts manufacturer chose a high-precision 5-axis CNC machine and paired it with efficient ultra-hard tools, successfully enhancing both machining precision and production efficiency. By utilizing these advanced machines, the company was able to boost production capacity without sacrificing precision.
- Technical Analysis: High-end machine tools typically come equipped with precise control systems and automated tool changes, allowing them to adjust machining parameters automatically to meet both precision and efficiency requirements in various processes.
-
Intelligent Control and Optimization
- With advancements in artificial intelligence (AI) and big data analytics, an increasing number of CNC machining facilities are adopting intelligent machining systems. These systems can monitor the machining process in real time, adjust cutting parameters through feedback and algorithms, and achieve the optimal balance of precision and efficiency.
- Case Study: A GT mold manufacturing company introduced an AI-optimized CNC machining system that could adjust cutting speed and feed rate in real time, improving production efficiency while maintaining mold precision and reducing lead times.
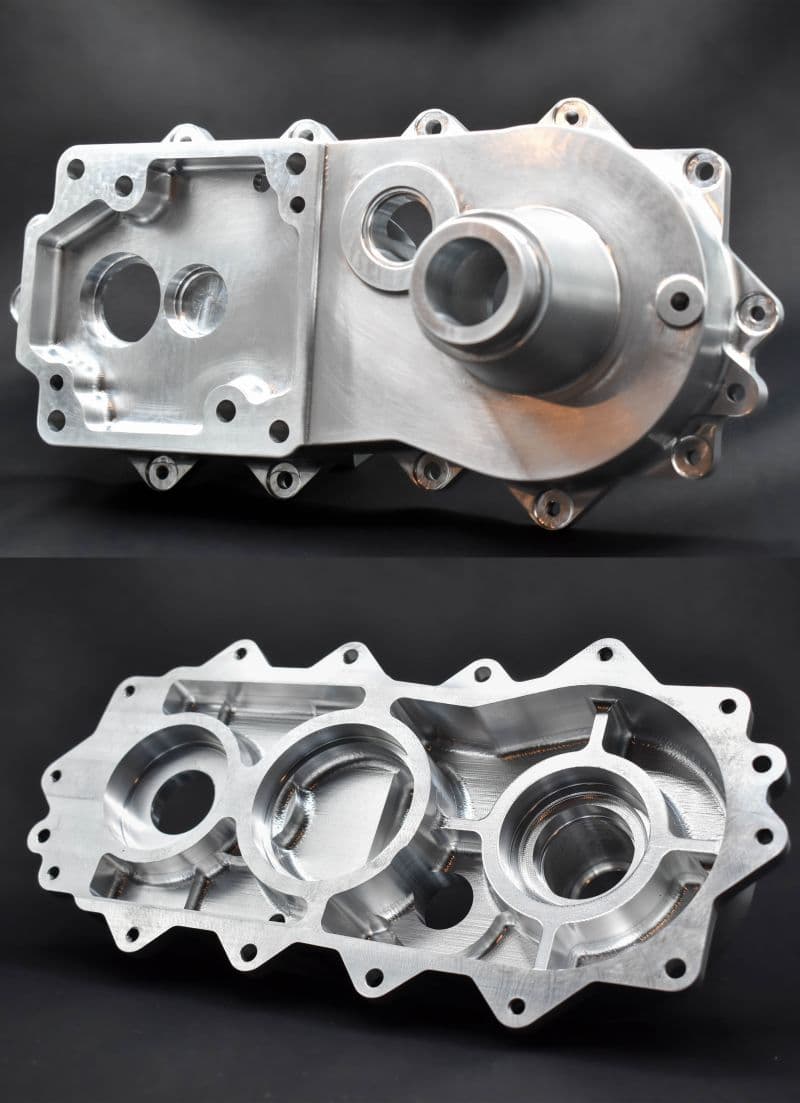
-
Cutting Process and Machining Parameter Adjustments
- By precisely controlling the cutting process and machining parameters, production efficiency can be maximized while ensuring accuracy. For example, selecting appropriate cutting depth, cutting speed, and feed rate can effectively reduce machining time and improve the overall quality of the workpiece.
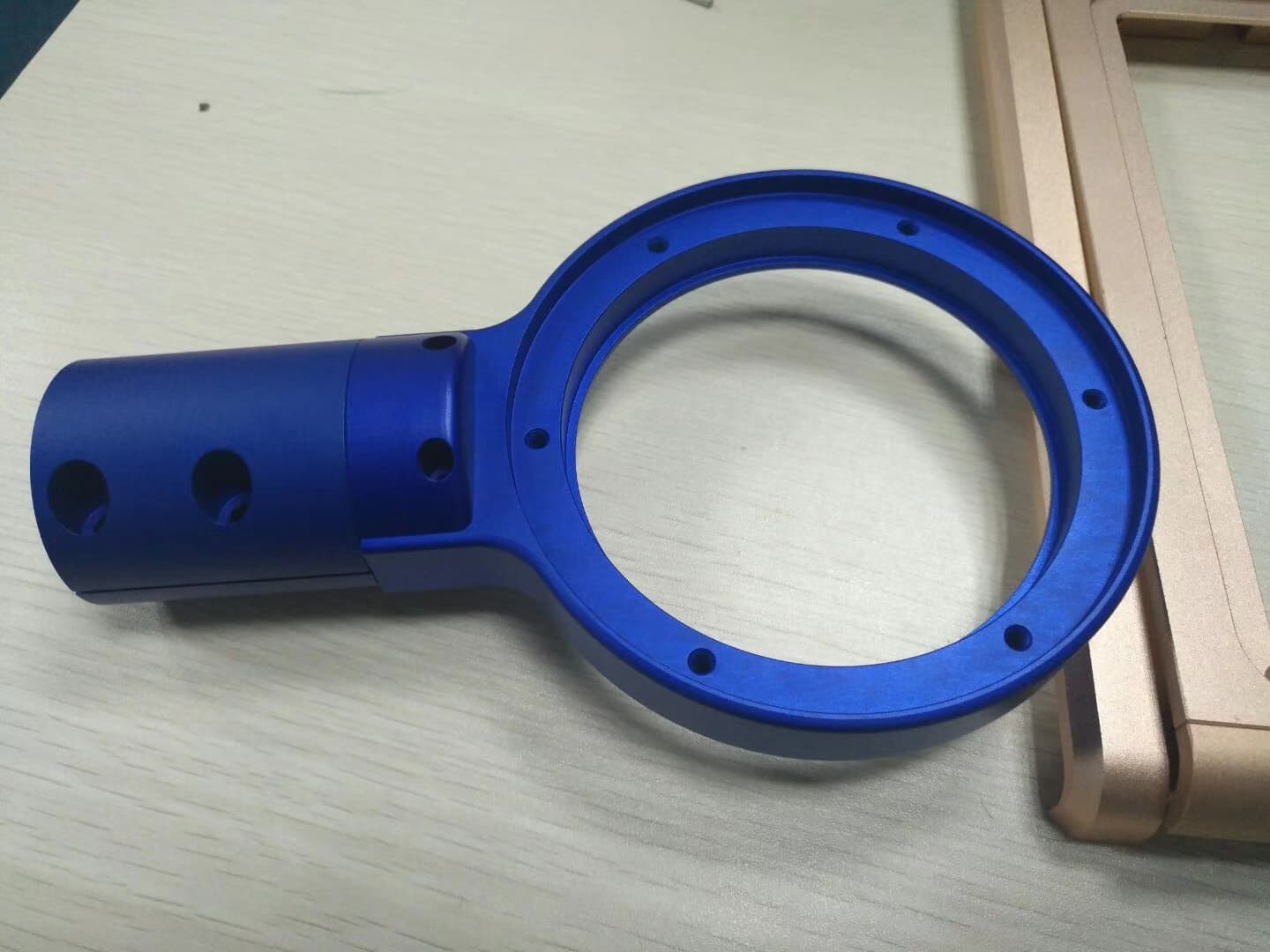
Industry Trends: The Fusion of Precision and Efficiency
With the rise of smart manufacturing and digitalized workshops, more and more CNC machining companies are adopting the "Industry 4.0" concept, using data and sensors to monitor the machining process in real time. This has made balancing precision and efficiency more flexible and adjustable, significantly enhancing the flexibility and controllability of production.
- Future Development: In the future, the application of AI and Internet of Things (IoT) technologies will enable CNC machining systems to automatically optimize the cutting process, improving efficiency while ensuring high precision. This will be a key trend in the development of the CNC machining industry.